Engager des dépenses significatives sans avoir au préalable étudié au minimum la faisabilité est vraiment dangereux. Aussi, je ne me lance jamais tête dans le guidon, sans faire un minimum de vérifications. L’approvisionnement le plus couteux est celui de la bobine de fil émaillé servant à bobiner les inducteurs. Aussi il me semblait impératif de réaliser un enroulement « pour voir ».
Le domaine des ampères-tours.
L’alimentation des inducteurs se faisant en courant continu, la limitation en intensité consommée n’est due qu’à la résistance ohmique du bobinage. On se doute que plus le fil est gros, plus faible est cette limitation et forte l’intensité qui en résulte. Hors la grandeur du champ magnétique généré est proportionnelle au nombre d’ampères-tours. Par exemple une spire parcourue par un courant d’un ampère crée exactement le même champ magnétique que 100 spires parcourues par 10mA. Aussi, pour ne commuter que des courants faibles qui de plus seraient compatibles avec la « sortance » des broches binaires de l’ATme328 la tentation d’utiliser un fil fin est grande … mais il faut les bobiner ces inducteurs et vous allez voir que c’est une sacré galère.
Disposant d’une quantité considérables de transformateurs basse tension de récupération, la première étape de cette opération d’évaluation à consisté à démonter la carcasse magnétique d’un petit transformateur 220V : Deux fois 12v 500mA. On aboutit à la réserve de fil gratuite montrée sur Image 02.JPG qui montre l’enroulement basse tension qui va servir à bobiner l’inducteur de validation. Bobiner, c’est enfantin dans le principe. On fait faire le tour du noyau à la réserve de fil. Mais dans notre cas, à chaque tour la grosse carcasse prismatique doit passer par le centre de l’ensemble. Autant dire que ce n’est pas une sinécure. Ne vous attendez pas à un bel enroulement à spires jointives. Par utilisation de ce fil de 0,4mm de diamètre, pas moins de 425 spires ont été enroulée. En 12V le courant continu qui la traverse fait deux ampères. Toutefois, ce courant ne sera appliqué que le huitième du temps, arrivant à un courant moyen de 250mA parfaitement compatible avec le fil utilisé. La puissance consommée sera de 3W, aussi il ne faudra pas faire fonctionner cette machine en permanence, mais lui ménager des périodes de refroidissement. Sur Image 03.JPG on peut observer le principe du bobinage. Il serait possible d’utiliser du fil plus petit. Par exemple du fil de 0,1mm de diamètre. On logerait alors 3400 spires par enroulement et le courant ne serait plus que de l’ordre de 200mA. NON ! Trop galère. Déjà qu’avec le fil de 0,4mm on va devoir se coltiner 3400 tournicotis pour les huit inducteurs. Alors on va en rester à cette solution « raisonnable ». ATTENTION : Avant de bobiner le premier enroulement, il faut assembler on l’avait deviné des deux demi-tores. Une fois le fil enroulé, l’ensemble devient indémontable. Aussi, avant de procéder au bobinage, il faut impérativement s’assurer que la bille peut se déplacer strictement sans problème sur les 360° du tore de guidage. Dans ce but, il faut impérativement éliminer la moindre petite bavure qui s’opposerait à la libre rotation de la bille. Quand le chemin de roulement est parfaitement lice sur les deux demi-tores, alors on assemble les deux pièces et l’on peut commencer à bobiner. Le résultat sur la Fig.4 montre que l’on a pas obtenu du spire contre spire, mais ce « vrac » un peu désordonné convient toutefois sans inconvénient. Les deux pièces ont été moulées en PLA translucide, car on désire voir se déplacer la bille. Sur le dessus, des orifices de 4mm tels que X ont été répartis tout le tour sur le corps du tore pour éventuellement faciliter l’observation des mouvements des billes.
Les autres bobinages du « magnétron ».
Impensable d’imaginer que nous allons bobiner les enroulements avec la technique utilisée sur le démonstrateur et montrée sur la Fig.4 ainsi que sur Image 3.JPG dans la <Galerie d’images>. Déjà l’internaute « lambda » ne disposera pas de transformateur pour en récupérer le fil émaillé. Et surtout, passer 425 fois le gros cube qui accroche partout à travers le noyau de la machine serait infiniment trop rébarbatif. On va donc approvisionner une bobine de 1kg de fil émaillé de 0,4mm de diamètre par l’entremise du commerce en ligne. C’est le « composant » de loin le plus coûteux dans notre projet. Je ne suis pas du tout très malin pour chercher sur Internet, et vous trouverez probablement pour moins onéreux. Toutefois, je cite ici ma source pour celles et ceux qui seraient encore moins débrouillards que moi : Cliquer ICI.
Disposer d’une belle bobine est une chose … s’en servir en est une autre. Nous sommes ici dans l’obligation de créer un « outil » qui va grandement faciliter notre travail qui de toute façon va imposer de la patience, du calme, de la sérénité et surtout de la patiente encore et encore. En effet, si une navette constitue la solution indispensable, elle nous inflige toutefois une « double pénalité » car avant d’entreprendre la réalisation d’un bobinage, il faut la remplir au préalable. On va en faire des tours et des tours. La préparation consiste à dérouler 25m de fil, et à les enrouler sur la navette. (Voir les calculs dans le cadre rose ci-dessous) Ensuite c’est cette dernière qui va environ 400 fois passer dans le noyau de l’ensemble et faire le tour par l’extérieur pour réaliser l’enroulement. Cette navette montrée sur la Fig.6 est dans la pratique une simple bobine un peu allongée sur laquelle on enroule tout le fil à bobiner dont l’une des extrémités est immobilisé dans le petit trou central. Les deux autres trous ne servent à rien et sont purement esthétiques. Les deux photographies Image 16.JPG et Image 17.JPG présentent ce petit outil réalisé à la demande avec mes techniques habituelles de façonnage et d’assemblage du polystyrène choc.
Sur https://www.amazon.fr/SWG-Fil-cuivre-%C3%A9maill%C3%A9-souder/dp/B07QD4Y6VR on trouve des bobines de 500g nettement moins couteuses, mais la longueur de fil n’est pas indiquée.
Pour celles et ceux qui le désirent, l’adresse du fournisseur pour les billes est ICI.
Étape n°1 : Concrétiser le magnétron.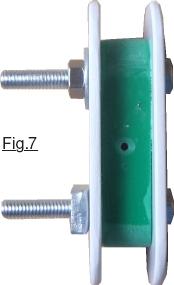
Travail de patience, il conditionne l’avenir du projet. La seule façon de vérifier la viabilité du concept et de l’aspect matériel que nous lui avons donné, c’est de franchir trois étapes incontournables qui vont nous assurer (Ou au contraire invalider !) que l’on arrive bien à faire tourner une bille à une rapidité suffisante pour qu’elle simule une particule à haute énergie :
• Étape n°1 : Bobiner les huit enroulements. (On se calme et l’on y va sans précipitation !)
• Étape n°2 : Réaliser un circuit électronique de commutation des courants inducteurs.
• Étape n°3 : Élaborer un programme « outil » avec Arduino pour piloter l’interface de puissance et déterminer les chronogrammes qui arrivent à accélérer correctement le projectile.
Initialement on va devoir bobiner 425 x 8 = 3400 spires en passant la nourrice de fil dans le centre du circuit magnétron. C’est un travail assez fastidieux. Aussi, pour ne par « projectiler » le dispositif par la fanêtre, il importe de s’y prendre avec méthode et surtout avec patience. Je vous conseille de limiter à un bobinage par jour le quota à ne pas dépasser. Commençons par « garnir » la navette. L’opération consiste à enrouler environ 36m de fil sur l’outil. Pour ma part, (Voir Image 21.JPG) j’ai vissé un petit piton dans le tronc d’un arbre mort dans l’espace extérieur de mon domicile. Puis, depuis ce point initial j’ai mesuré 36m en reportant environ sept fois au sol la longueur d’un « mètre à ruban de 5m ». Comme montré sur la Fig.7 la navette a été munie d’une poignée constituée de deux boulons de diamètre nominal 5,5mm. On peut ainsi la tenir fermement avec la main gauche pendant que la main droite enroule le fil émaillé. On attache le fil émaillé sur le petit piton, on enfile un tournevis dans le centre de la bobine de cuivre comme le montre la Fig.8 et on déroule allègrement et dans la joie les 36m jusqu’au repère de longueur piqueté dans le sol. On coupe le fil et sans le lâcher, on enroule le film plastique élastique autour de la bobine pour la sécuriser. Enfin on enfile l’extrémité du fil émaillé dans le petit trou central de la navette pour le bloquer, et on enroule les 36m autour du noyau de l’outil. Durant cette opération ne pas tirer sur le fil. Il suffit de l’enrouler et le tendre, le juste ce qu’il faut pour obtenir le résultat de la Fig.9 qui prouve que l’on arrive aisément à un bobinage relativement régulier. On constate que le volume possible d’enroulement sur le noyau est nettement plus important que celui nécessaire. Au départ il était difficile d’évaluer les dimensions idoines. Aussi c’est volontairement que la navette a été surdimensionnée. On peut noter que ce n’est pas un inconvénient vu qu’ainsi exagérée elle reste suffisamment petite pour
passer dans le centre de la structure du cyclotron. Du reste, plus le noyau de la navette est important, et moins le fil sera cintré dans cet enroulement provisoire, ce qui est favorable à sa bonne santé. À ce stade on libère le fil émaillé et on retire les deux boulons qui servaient de poignée. On passe le fil dans le petit trou du flanc de l’une des joues d’enroulement. On en fait dépasser d’environ 50cm pour prévoir la liaison avec les circuits électronique de commutation et avec calme et pondération on bobine spire à spire jusqu’à épuiser le contenu de la navette dont 50cm des extrémités seront prévus pour la ligne de branchement extérieure. Durant cette opération, veiller à enrouler de façon homogène, le spire contre spire serait idéal, mais vu les circonstances on se contentera d’une régularité globale ressemblant à celle de la Fig.9 ci-contre. Quand avec patience et sérénité on a garni entièrement l’un des bobinages, on « cache » les deux fils de liaison en les enroulant entre deux inducteurs et en les immobilisant avec du ruban adhésif. Il n
e reste plus qu’à recommencer sept fois dans les jours qui vont suivre. Vive l’électromagnétisme !
Bobiner les 35m de fil émaillé pour chaque inducteur.
C’est de loin l’opération la plus indigeste de la réalisation de ce petit projet ludique. Ce chapitre va en détailler certains aspect qui méritent d’être soulignés. Toutefois, avant d’utiliser la navette de la Fig.9 sur laquelle les deux boulons de saisie ont été enlevés, revenons à l’assemblage de la structure. Les deux demi-goulottes ont été moulées en 3D. Ce modèle présente des difficultés particulières, notamment les joues des inducteurs qui ne font que 1mm d’épaisseur. Il en résulte des « dentelures » à la périphérie qui sont visibles sur les photographies. Il faut avec une lime éliminer toutes ces aspérités pour ne pas que le fil accroche lors du bobinage. Par ailleurs, comme indiqué sur Image22.JPG l’orientation du moulage en 3D privilégie un chemin de roulement situé vers le haut pour ne pas qu’il soit entièrement rempli de petites cloisons support, car le tore de circulation doit être parfaitement lisse. Du coup, on retrouve de telles cloisons support dans le volume qui sera occupé par le fil émaillé des inducteurs, laissant des aspérités lorsqu’elles sont enlevées. Il sera donc important de limer ces traces résiduelles parasites. Malgré l’orientation de la pièce au moulage, on trouvera comme visible sur Image 23.JPG de minuscules petites aspérités dans la goulotte de circulation des billes. Ces petits défauts ne sont pas très nombreux, mais il faut absolument les polir avec du papier abrasif. S’assurer de la circulation parfaite des billes quand on aura achevé cette opération. Par ailleurs, sur l’imprimante 3D on peut avoir une minuscule différence d’élongation sur X et sur Y engendrant une toute petite différence dans les cotes Dx et Dy. Même si cette différence est minime et inférieure à 0,1mm, il importe d’orienter le dessus et le dessous pour faire correspondre les élongations et mettre en phase les différences d’étirement. Lorsque l’orientation la plus favorable est trouvée, comme le montre Image 24.JPG on repère la correspondance. Ce n’est qu’en respectant ce détail que les joues latérales des bobinages qui ne font qu’un millimètre d’épaisseur seront en parfaite correspondance verticale.
Force est de constater sur la Fig.11 qui représente la structure complètement assemblée avant de commencer les diverses opérations de bobinage, que contrairement à ce que montre la Fig.4 elle est devenue bicolore ! En fait, lorsque le support coudé du collisionneur à été collé à l’Araldite sur le dessus, un petit résidu de colle à coulé dans le passage des billes. Cet obstacle étant plus loin que le coude, il était impossible de l’éliminer. Il a donc fallu tout recommencer à zéro. Le filament translucide qui me restait était insuffisant pour mouler le dessus et le dessous. La structure inférieure est alors violette et la machine devient bicolore !
Toujours dans le cadre de la préparation avant les opérations de bobinage, il faut s’assurer que la bille circule parfaitement dans le tunnel du collisionneur. En particulier si vous optez pour la version inclinée avec les deux aimants de sustentation. À l’intérieur du manchon d’accouplement, il y a des cloisons support que l’on doit éliminer. C’est également vrai pour la version verticale de la Fig.19 si vous optez pour la solution sans aimants permanents. Avec une pince et un cutter on enlève ces cloisons support, puis avec une petite lime on élimine les résidus. Enfin, comme symbolisé sur la Fig.12 avec du papier abrasif enroulé on lisse parfaitement le conduit, qu’il soit coudé ou rectiligne. On s’assure de la parfaite circulation des billes dans le dispositif qui alors est pleinement validé.
Assemblons la structure de la machine après avoir totalement ébavuré le dessus et le dessous du tore, réalésé tous les trous d’observation du passage des billes dans leur chemin de circulation, et ceux de traversée des vis d’immobilisation. On vérifie une dernière fois que le manchon de liaison du collisionneur est strictement sans bavure comme sur la Fig.13 et que l’on peut facilement récupérer les billes avec un quelconque aimant permanent dans l’ouverture prévue à cet effet sur le coté opposé au collisionneur. À ce stade du projet on peut encore tout redéposer si c’est nécessaire. Aussi, vérifier une dernière fois que les billes se déplacent parfaitement dans le tore. Alors on peut commencer à bobiner.
Montré sur la photographie d’Image 25.JPG on utilise à convenance l’un des deux trous pratiqué au raz du noyau sur les joues de la bobine pour faire sortir le fil émaillé. On en fait dépasser environ quarante centimètres qui serviront à la liaison électrique vers le module électronique de commutation. Puis on enroule cette ligne électrique dans le voisinage de l’inducteur qui va être bobiné. On immobilise comme l’on peut, avec du ruban adhésif par exemple, ce fil qui ne devra pas « exister » durant les opérations d’enroulement du fil sur les bobines. Attention, à partir de ce stade la structure est indémontable, ou il faudrait débobiner tous les inducteurs ce qui reste totalement impensable.
Dans la pratique, enrouler les 35m de fil émaillé pour chaque inducteur s’avère bien moins indigeste que je ne l’avais supposé. Surtout garder le fil tendu durant toute l’opération. Par utilisation de la navette, il faut moins d’une heure et demie par enroulement. Aussi, j’ai réalisé deux inducteurs par jour pour ne pas saturer. Lorsque un inducteur est terminé, j’enroule la deuxième extrémité avec la première et termine l’opération en collant cette sortie externe avec de l’Araldite comme sur Image 26.JPG.
La suite est ici.